Benefits and Drawbacks of Tiling to a Calcium Sulphate Screed
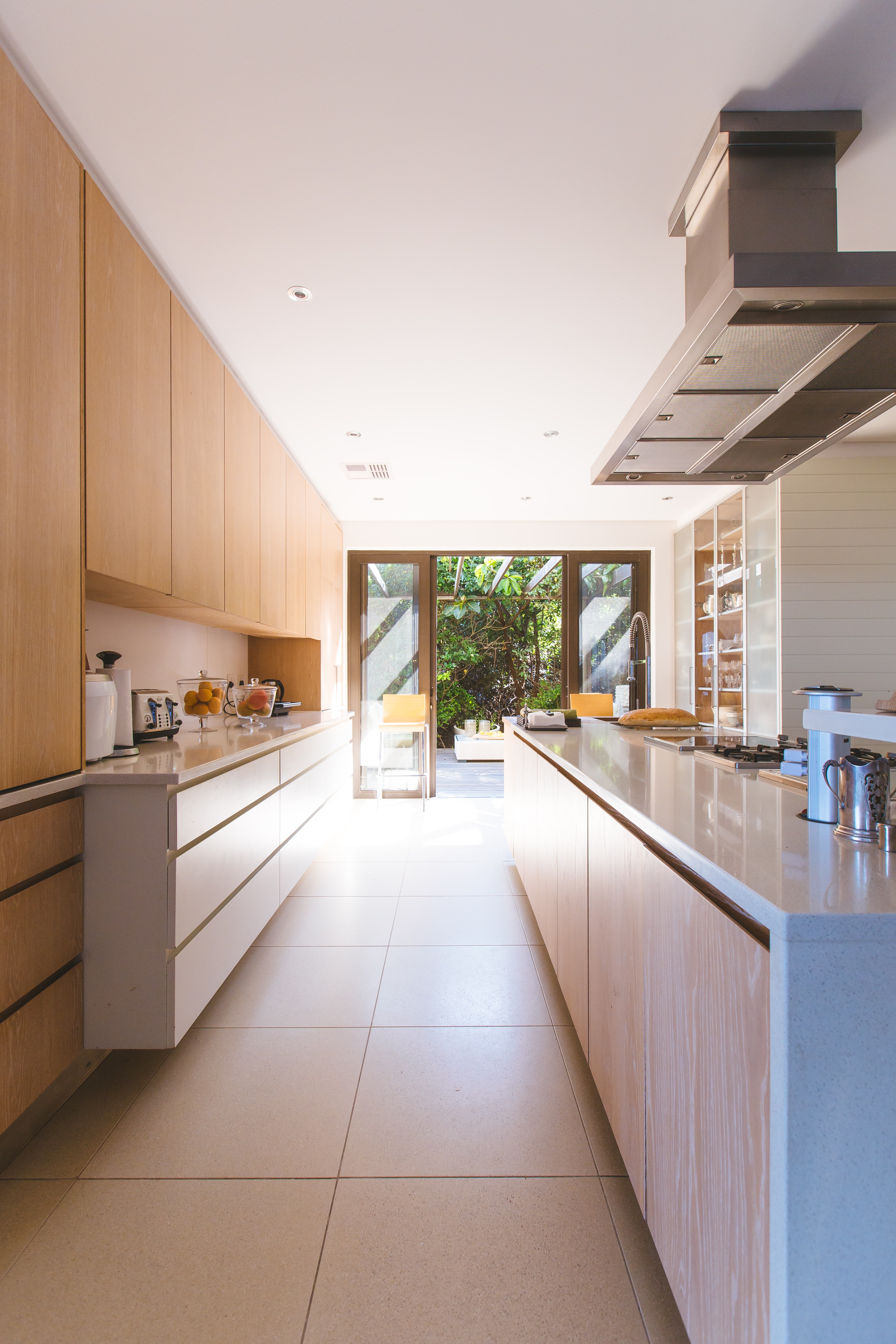
While there are many benefits associated with anhydrite screeds, tradespeople and project man-agers must be aware of the potential failures and must be proactive to ensure that they are correctly prepared by screed contractors prior to tile installation.
Specialist Ceramics are always seeking out ways to do things better and further raise the working standards in our industry. We appreciate that no two projects are alike and that every square metre deserves meticulous attention to detail, from concept to hand over. That’s why, we are passionate about working in collaboration with our clients by providing undivided technical expertise and professionalism at every point of contact.
At Specialist Ceramics, we believe in getting everything right the first time. We are committed to raising the bar and always striving for best practice.
We have noticed an increased demand for CS Screeds and a lack of understanding about them within the building industry due to their relatively new emergence as an alternative to traditional screeds.
There are some important practices that can be applied to ensure the integrity of tiling over a CS screed. The use of primer after the screed is dry, dust and laitance free is highly effective in creating more stable surface and better bondage of tile adhesive.
Priming the screed also functions as a preventative barrier against moisture migration and the chemical reaction of ettringite, when cement in a tile adhesive reacts with the gypsum in the anhydrite screed, forming mineral crystals at the interface which can cause de-bonding.
As construction technology continues to develop, we are seeing calcium sulphate products that contain lower levels of laitance. Alternative pump-able cement-based screeds are also proving to gain traction and success in other countries abroad, without the need for surface preparation be-fore tile.
Benefits of Calcium Sulphate Screeds
When installed correctly and properly managed, calcium sulphate (CS) screeds offer substantial benefits in larger areas when compared to traditional sand-cement screeds. They are a highly cost-effective and functional option for covering large areas and non-wet areas more than 40m2.
Calcium sulphate screeds are faster to install due to the ability to pump the screed in as a liquid. The pump-able screed is also self-levelling, so the finished product is precisely level, stable and compact with minimal shrinkage. The self-levelling nature also makes it suitable for going over existing surfaces that may be uneven. Hence, CS screeds are not suited or recommended for wet areas that require slopes or drainage.
They are the screed of choice for covering underfloor heating (UFH) systems. CS screeds require no physical compaction meaning less manual labour which equates to less disturbance to the UFH system and less chance of damage during installation.
The liquid form of CS screeds makes it ideal for UFH because it envelopes the pipes to eliminate voids. It also enhances heat transfer between the pipes and the floor due to reduced thickness re-quired with CS screeds, adding more value to the structure of the building. Additionally, because CS screeds are considered to be a more environmentally friendly products because it is typically comprised of approximately 35% recycled industrial by-products.
Drawbacks of Calcium Sulphate Screeds
Prior to tile installation, removing laitance is one of the most critical preparation requirements of a CS screed which is usually undertaken as the responsibility of the screed contractor. Laitance is a fragile layer of fine particles deposited on the surface of the screed as the anhydrite cures.
The process of removing laitance usually requires use of a suitable sanding machine 4-6 days af-ter screed installation to scarify the surface layer. Laitance must be removed to ensure proper bonding of the tile adhesive to the screed and can assist with the drying process.
Note: The presence of laitance when left on the surface of screed will lead to failures in tile installation.
CS screeds have longer drying times than traditional Portland cement screeds. As recommended by manufacturers, a typical CS screed dries at a rate of 1mm/day for the first 40mm and a further 0.5mm a day for anything thicker. For example: 45mm screed will need a minimum of 50 days be-fore being ready for tile.
The drying of CS screeds are also highly dependant upon optimal drying conditions that are best at 20°C, low air humidity and adequate ventilation. Hence, the drying out process is another factor that must be smartly managed and maintained. In some special cases, it is possible to speed up the drying process using dehumidifiers. Drying of screeds can be greatly influenced by individual site conditions.
Forced Drying
When an underfloor heating system is installed into a screed, the process of force drying can be applied through the use of a ‘hot and cold cycle”, which can be initiated seven days after installa-tion. This requires that the UFH put through a full cycle of the heating range. This process can as-sist with the drying process and ascertain operation of the system and structural integrity of the screed.
Technically known as ‘commissioning’ (heating and cooling procedure) of underfloor heating sys-tems. The process involves setting the UFH temperature to 20-25C, maintaining it a minimum of 24 hours and then gradually increase the temperature in 5C increments to maximum operating temperature. This should be maintained for a further seven days (water temperature should not ex-ceed 55C for screeds), prior to returning to ambient temperature again in 5C increments. Then the system should be turned off for 48 hours prior to moisture testing of the screed.
Space heaters and dehumifiers may also be used to force dry CS screeds. An industrial closed-circuit systems is recommended and must be carefully managed to ensure no water spills.
After drying the screed, the residual moisture content must be determined using one of the ap-proved test methods - hair hygrometer, carbide bomb or oven dry tests to demonstrate suitability for acceptance of floor finishes.
Our passion is directed to deliver technical expertise and a professional ser-vice at every point of contact. Thats why, we are consistently going above and beyond our clients expectations to ensure best practice.
Weighing It All Up
Calcium sulphate screeds are a cost-effective and reliable choice for large scale areas, especially when coupled with underfloor heating. We encourage developers, project managers, builders and quantity surveyors to seek technical advice from experienced screed contractors.
For the foreseeable future, traditional sand-cement screeds will continue to be an economic and functional choice for smaller rooms and wet areas that require fall for drainage.
Specialist Ceramics is London and South UKs most trusted and preferred low-risk tile contractor for large scale projects.